Don't miss our holiday offer - 30% OFF!
Advanced Coating Techniques For Enhancing Durability And Efficiency In Jaw Crushers: A Comprehensive Guide
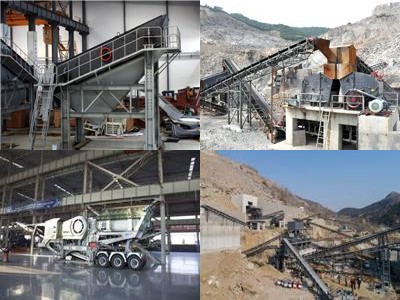
In the demanding world of heavy industrial equipment, the longevity and efficiency of machinery are paramount. Jaw crushers, pivotal in the crushing process, face significant operational challenges due to the harsh environments they operate in. At Zenith, we understand these challenges and advocate for the use of advanced coating techniques to enhance the durability and efficiency of these critical components. This comprehensive guide delves into the sophisticated world of coatings, offering insights into how they can revolutionize the performance of jaw crushers.
Introduction to Jaw Crusher Coating Techniques
Jaw crushers are essential in the mining and construction industries for breaking down large rocks into smaller, manageable pieces. However, the extreme conditions under which they operate can lead to rapid wear and tear, reducing their efficiency and lifespan. Advanced coating techniques have emerged as a solution, offering a protective layer that significantly enhances durability and operational efficiency. This guide aims to explore these techniques, shedding light on their importance and the objectives they aim to achieve in jaw crusher maintenance and performance enhancement.
Understanding the Basics of Coating Materials
The choice of coating material is crucial in determining the effectiveness of the protective layer applied to jaw crushers. Commonly used coatings include thermal spray, polymer-based, and ceramic coatings, each with unique properties tailored to combat specific challenges. Ideal coating materials exhibit high wear resistance, thermal stability, and the ability to withstand mechanical stresses. This section compares traditional coatings with advanced alternatives, highlighting the superior protection and performance enhancements offered by the latter.
Advanced Coating Techniques for Jaw Crushers
Advancements in coating technology have introduced several innovative solutions for jaw crusher protection. Thermal spray coatings, for instance, provide a versatile and effective barrier against wear and corrosion. Polymer-based coatings are celebrated for their exceptional wear resistance, while ceramic coatings offer unmatched protection in high-temperature environments. These advanced techniques not only extend the service life of jaw crushers but also contribute to the overall efficiency of the crushing process.
Application Process and Best Practices
The application of coatings on jaw crushers involves meticulous preparation and precise execution to ensure maximum adhesion and effectiveness. Surface preparation, including cleaning and roughening, is critical for optimal coating adherence. Following a detailed step-by-step guide for coating application can significantly enhance the protective layer’s performance. Regular maintenance and inspection are essential to sustain the benefits of coated jaw crushers, ensuring they continue to operate at peak efficiency.
Case Studies and Real-World Applications
The practical benefits of advanced coating techniques are evident in numerous success stories across the heavy machinery industry. Comparative analyses reveal that coated jaw crushers exhibit significantly lower wear rates and longer operational lifespans than their uncoated counterparts. Furthermore, ongoing research and development in coating technologies promise even greater advancements, potentially setting new standards for durability and efficiency in heavy industrial equipment.
The relentless pursuit of efficiency and durability in the heavy industrial sector has led to significant advancements in coating technologies for jaw crushers. At Zenith, we are at the forefront of this innovation, offering a range of crushers, mills, and related equipment designed to meet the highest standards of performance and longevity. By embracing advanced coating techniques, we empower our clients to achieve unparalleled operational efficiency and equipment durability, ensuring their machinery withstands the test of time and the rigors of heavy-duty use.