Don't miss our holiday offer - 30% OFF!
How Crucial Is A Crusher In Mining Operations?
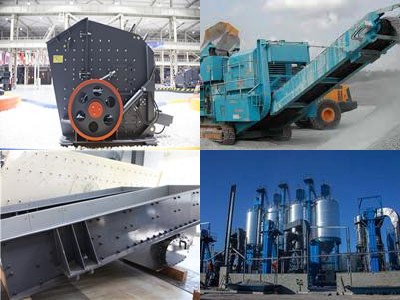
Crushers are indispensable machinery in the mining industry, playing a pivotal role in the extraction and processing of minerals. The efficiency and effectiveness of crushers can significantly impact the productivity and profitability of mining operations. As a leading provider of heavy industrial equipment, Zenith specializes in offering advanced crusher solutions that cater to diverse mining needs. In this article, we delve into the critical importance of crushers in mining operations, exploring their varied types and specific applications, while also evaluating the efficiencies and costs associated with different crusher models.
The Role of Crushers in Modern Mining Processes
Crushers serve as the first step in the mineral processing chain, responsible for reducing large rocks and ore into smaller, manageable sizes. This size reduction is a crucial part of mining, as it facilitates subsequent processing stages such as milling, beneficiation, and material handling. Without effective crushing, the efficiency of these downstream operations would be severely compromised, leading to increased operational costs and reduced overall productivity.
In modern mining processes, crushers are used in both surface and underground operations. Surface mining typically involves larger and more powerful crushers to handle the high volume of material extracted, while underground mining employs smaller, more specialized crushers that fit within the limited space of underground tunnels. Regardless of the setting, the primary goal remains the same: to convert raw material into a form that can be further refined and processed.
At Zenith, we understand the integral role that crushers play in mining operations. Our range of crushers is designed to meet the challenges of modern mining, offering robust and reliable performance to ensure optimal material processing. From primary jaw crushers to advanced cone crushers, our products are engineered to deliver superior crushing efficiency and durability.
Types of Crushers and Their Specific Applications
Crushers come in various types, each designed for specific applications within the mining sector. The most common types of crushers are jaw crushers, cone crushers, and impact crushers, each serving distinct purposes based on the nature of the material being processed and the desired output size.
Jaw crushers are typically used for primary crushing, where large rocks are broken down into smaller, more manageable sizes. They are known for their ability to handle tough and abrasive materials, making them ideal for mining operations involving hard rock and ore. Zenith’s jaw crushers are renowned for their high crushing ratios, robust construction, and efficient operation.
Cone crushers, on the other hand, are commonly used for secondary or tertiary crushing. They work by compressing the material between a moving piece of steel and a stationary piece of steel, which finely breaks down the material into the desired size. Zenith’s cone crushers are designed to provide high productivity and excellent product shape, making them essential for producing high-quality aggregate from mined materials.
Impact crushers are used when the goal is to achieve precise shaping and size reduction in the final product. They are particularly effective for handling softer materials and are known for producing uniform particle sizes, which are crucial for certain industrial applications. Zenith’s impact crushers are engineered to offer robust performance and versatility, suitable for a variety of mining applications.
Evaluating the Efficiency and Cost of Various Crushers
Efficiency in mining operations is paramount, and the choice of crusher significantly impacts overall performance and cost-effectiveness. Efficiency is often measured in terms of throughput, energy consumption, and the consistency of the particle size produced. Cost considerations include both the initial capital investment and ongoing operational expenses such as maintenance, energy consumption, and wear part replacement.
Jaw crushers, with their high crushing ratios and durable design, are considered highly efficient for primary crushing stages. They generally require lower operating costs due to their simple structure and fewer wear parts. However, their efficiency can be influenced by the hardness and abrasiveness of the material being processed.
Cone crushers, known for their high output and fine adjustment capabilities, are efficient for secondary and tertiary crushing stages. They offer a good balance between throughput and energy consumption. The initial cost of cone crushers might be higher than jaw crushers, but their efficiency and lower operating costs often justify the investment over time.
Impact crushers, while versatile and efficient in producing uniform particle sizes, may incur higher operating costs due to frequent wear part replacements. Their efficiency largely depends on the material type and the specific application requirements. However, when precision and specific sizing are priorities, their operational efficiency can outweigh the costs.
Crushers are a fundamental component in the mining industry, essential for ensuring smooth and efficient mineral processing operations. Understanding the role, types, and efficiency evaluations of crushers is crucial for optimizing productivity and profitability in mining activities. Zenith, with its extensive range of advanced crushers, provides reliable solutions that meet the complex needs of modern mining operations. By investing in Zenith crushers, mining operations can achieve higher efficiency, reduced operational costs, and increased output quality. Contact Zenith today to learn more about how our crushers can enhance your mining projects and drive success.