Don't miss our holiday offer - 30% OFF!
How Do Primary And Secondary Crushing Processes Differ?
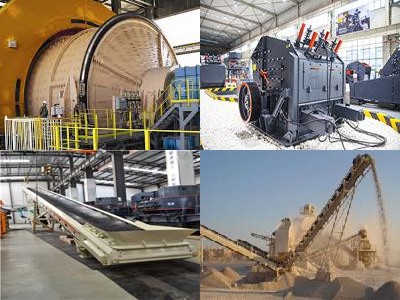
Primary and secondary crushing are critical stages in the mineral processing and aggregate production industries. These processes are essential for preparing raw materials for further refining or utilization, impacting both the efficiency and quality of the final product. At Zenith, we are committed to providing high-quality crushing solutions that meet your specific needs. Understanding the differences between primary and secondary crushing can help you choose the right equipment and optimize your operations.
Understanding Primary Crushing: The Initial Stage
Primary crushing is the first stage in the material reduction process. It involves the initial breaking down of large rocks and raw materials into smaller, manageable sizes. This stage is crucial as it sets the foundation for the subsequent processing stages. Typically, primary crushers such as jaw crushers, gyratory crushers, and impact crushers are used to handle large feed sizes and high-capacity materials.
One of the key characteristics of primary crushing is its ability to handle large, abrasive materials. The goal is to reduce the material to a size that can be easily transported and processed by the secondary crusher. The primary crusher’s robust construction and ability to handle high-stress loads make it suitable for heavy-duty applications. At Zenith, we offer a range of primary crushers designed to meet the demands of various applications, ensuring optimal performance and durability.
In addition to size reduction, primary crushing also aims to improve material flow within the processing plant. Efficient primary crushing can minimize blockages and bottlenecks, ensuring a smooth and continuous operation. By investing in high-quality primary crushers from Zenith, you can enhance your plant’s productivity, reduce downtime, and achieve better overall efficiency.
Secondary Crushing: Enhancing Material Quality
Secondary crushing follows the primary crushing stage and further reduces the size of the material. This stage is essential for producing materials of specific sizes and shapes required for various applications. Secondary crushers, such as cone crushers, impact crushers, and hammer mills, are used to achieve finer granulation and improve the quality of the final product.
One of the primary goals of secondary crushing is to achieve a consistent and uniform particle size. This is particularly important for industries such as construction, where material specifications are stringent. Zenith’s range of secondary crushers is designed to provide precise, reliable, and efficient performance, ensuring that your material meets the required standards.
In addition to size reduction, secondary crushing also plays a role in improving the material’s overall quality by removing impurities and enhancing its structural integrity. By using advanced technology and innovative designs, Zenith’s secondary crushers can deliver high-quality end products that meet the demands of various industries. Investing in our secondary crushing solutions can help you achieve superior material quality and enhance your production processes.
Key Differences Between Primary and Secondary Crushing
The primary difference between primary and secondary crushing lies in the stage at which they occur. Primary crushing is the initial stage of the material reduction process, where large rocks and raw materials are broken down into smaller sizes. In contrast, secondary crushing takes place after primary crushing and focuses on further reducing the material size to meet specific requirements.
Another key difference is the type of equipment used in each stage. Primary crushers are designed to handle large, abrasive materials and operate under high-stress conditions. They are typically heavy-duty machines such as jaw crushers, gyratory crushers, and impact crushers. On the other hand, secondary crushers are used to achieve finer granulation and improve material quality. These machines, including cone crushers, impact crushers, and hammer mills, are designed for precision and efficiency.
The goals of primary and secondary crushing also differ. Primary crushing aims to reduce the material to a manageable size for further processing and ensure smooth material flow within the plant. Secondary crushing, however, focuses on achieving specific material sizes and enhancing the quality of the final product. By understanding these differences, you can choose the right equipment for each stage and optimize your crushing processes.
In conclusion, understanding the differences between primary and secondary crushing is crucial for optimizing your material processing operations. By choosing the right equipment for each stage, you can achieve better efficiency, higher productivity, and superior material quality. At Zenith, we offer a comprehensive range of primary and secondary crushers designed to meet the diverse needs of various industries. Our commitment to innovation, quality, and customer satisfaction ensures that you receive the best solutions for your crushing requirements. Contact Zenith today to learn more about our products and how we can help you achieve your operational goals.