Don't miss our holiday offer - 30% OFF!
How Does An Impact Stone Crusher Differ From Other Types?
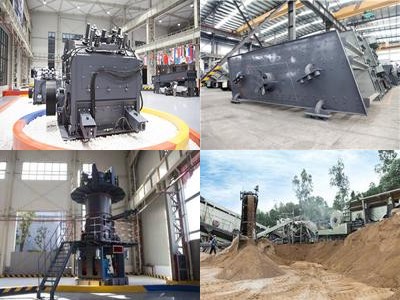
The field of crushing equipment encompasses a diverse range of machines, each designed to handle specific types of materials and produce certain outcomes. Among these, the impact stone crusher stands out for its distinctive approach to breaking down rocks and stones. As a leading provider of industrial equipment, Zenith offers an array of impact stone crushers tailored to meet various operational needs. This article aims to explore the unique aspects of impact stone crushers, draw comparisons with other common types such as jaw crushers, and discuss their respective advantages and disadvantages.
Introduction to Impact Stone Crushers
Impact stone crushers operate by employing a high-speed rotor that throws stones against a stationary surface or impact plates, causing them to shatter and break apart. This process takes advantage of the stone’s compressive strength and results in a highly efficient method of crushing. Zenith, renowned for its industrial equipment, provides advanced impact crushers designed to handle a wide range of materials, from soft minerals to hard stones.
Typically used in both primary and secondary crushing stages, impact crushers offer versatility and high reduction ratios. They are particularly advantageous for producing uniform, cubical-shaped aggregates which are ideal for numerous construction applications. The user-friendly design and maintenance of Zenith’s impact crushers allow for easy integration into various production lines.
Furthermore, the impact crusher is integral in sectors like mining, quarrying, and recycling, where material size reduction is critical. Zenith’s impact crushers, engineered with precision and durability, address these needs effectively, ensuring optimal performance across projects.
Key Features of Impact Stone Crushers
One of the distinguishing features of impact stone crushers is the use of hammers or blow bars attached to a high-speed rotor. These hammers propel the stones against impact plates, breaking them into smaller pieces. Zenith’s impact crushers utilize high-quality, wear-resistant materials ensuring durability and longevity.
Another key feature is the adjustability of the crusher’s settings, allowing operators to control the size of the final product. This is achieved through the variation of rotor speed and the arrangement of impact plates. Zenith’s models are designed with user convenience in mind, providing quick adjustment mechanisms to meet different project requirements.
In addition, impact crushers are equipped with safety measures to protect both the machinery and operators. Emergency stop functions, automated systems to detect uncrushable materials, and easy access for maintenance are integral to Zenith’s design philosophy, ensuring high operational safety and efficiency.
Comparison with Jaw Crushers: Differences in Design and Operation
Jaw crushers and impact crushers serve similar purposes but differ significantly in design and operation. Jaw crushers use compressive force to break down stones by squeezing them between two rigid surfaces, whereas impact crushers use the principle of rapid impact to fracture stones. Zenith provides both types of crushers, offering solutions based on project-specific needs.
Design-wise, jaw crushers typically have a simpler build, consisting of a stationary and a movable jaw. In contrast, impact crushers feature a complex design with a high-speed rotating rotor, impact plates, and hammers. This complexity allows impact crushers to produce finer and more uniformly shaped end products compared to jaw crushers.
Operational differences extend to the stages of crushing: jaw crushers are generally used for primary crushing to reduce material to a manageable size for secondary processing. Impact crushers, on the other hand, can perform both primary and secondary crushing, making them more versatile. Zenith’s portfolio includes robust jaw and impact crushers, ensuring customers find the right equipment for their specific applications.
Advantages and Disadvantages of Impact Stone Crushers
A notable advantage of impact crushers is their ability to produce fine and uniform aggregates, which are highly desirable for concrete production and road construction. The versatility and high reduction ratios of Zenith’s impact crushers make them suitable for a wide range of applications, from mining to recycling.
Another benefit is the ease of adjusting settings to control product size, along with a typically lower operational cost due to high efficiency. Zenith’s impact crushers are designed for minimal downtime, with easy maintenance features ensuring sustained productivity and reliable performance.
However, there are some disadvantages to consider. Impact crushers can experience higher wear and tear, meaning parts may need frequent replacement, especially when dealing with very abrasive materials. Additionally, these crushers might not be suitable for very hard stone types, which could cause potential damage. Zenith addresses these concerns with high-quality, wear-resistant materials and designs built for durability, ensuring long-term use with reduced maintenance needs.
Impact stone crushers offer unique advantages that make them essential in various industries, particularly in achieving fine, uniform aggregates. As a leading industrial equipment provider, Zenith supplies top-tier impact crushers engineered for efficiency, versatility, and durability. The variety of features and operational benefits coupled with our commitment to high-quality manufacturing ensure that our impact crushers meet the demanding needs of today’s industrial applications. If you’re seeking reliable, high-performance crushing solutions, look no further than Zenith’s range of impact stone crushers.