Don't miss our holiday offer - 30% OFF!
How Effective Is A Rock Crusher In Making Gravel?
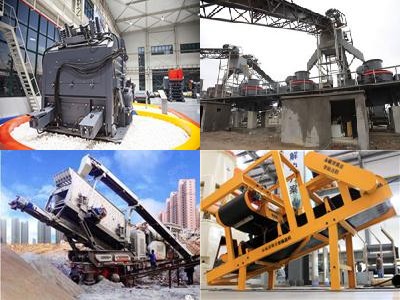
Rock crushers play a pivotal role in the production of gravel, a fundamental material in construction and landscaping. At Zenith, we specialize in providing high-quality rock crushers and other heavy industrial equipment designed to meet the rigorous demands of gravel production. This article delves into the mechanics, types, efficiency, and environmental impact of rock crushers, highlighting how Zenith’s products excel in these areas.
The Mechanics of Rock Crushers: Breaking Down the Process
Rock crushers operate by applying mechanical force to break down large rocks into smaller, more manageable pieces. The process begins with the feeding of raw material into the crusher, where it is subjected to intense pressure and impact. The primary mechanism involves a combination of compression and shearing forces, which fracture the rock along its natural fault lines. This initial stage is crucial for reducing the size of the material to a level that can be further processed.
The crushing process typically involves several stages, starting with primary crushing, where large rocks are reduced to a size that can be handled by secondary crushers. Secondary crushers further reduce the size of the material, making it suitable for tertiary crushing, which produces the final gravel product. Each stage employs different types of crushers, such as jaw crushers for primary crushing, cone crushers for secondary crushing, and impact crushers for tertiary crushing.
Zenith’s rock crushers are engineered to optimize the crushing process, ensuring maximum efficiency and minimal wear and tear. Our crushers are equipped with advanced features such as hydraulic adjustment systems, automated control systems, and robust construction materials, which enhance their performance and longevity. By investing in Zenith’s rock crushers, customers can achieve superior gravel production with reduced operational costs.
Types of Rock Crushers: Which is Best for Gravel Production?
There are several types of rock crushers, each designed for specific applications and material characteristics. The most common types include jaw crushers, cone crushers, impact crushers, and gyratory crushers. Each type has its unique advantages and is suited for different stages of the crushing process.
Jaw crushers are typically used for primary crushing due to their ability to handle large, hard materials. They operate by compressing the rock between a fixed and a moving jaw, which breaks it down into smaller pieces. Cone crushers are used for secondary crushing and are known for their ability to produce a uniform particle size. They work by crushing the rock between a rotating cone and a fixed outer wall.
Impact crushers are ideal for producing high-quality gravel with a cubical shape. They use high-speed impact force to break the rock into smaller pieces, making them suitable for tertiary crushing. Gyratory crushers, similar to jaw crushers, are used for primary crushing but are capable of handling larger capacities and producing finer output.
Zenith offers a comprehensive range of rock crushers, including jaw crushers, cone crushers, and impact crushers, each designed to meet the specific needs of gravel production. Our crushers are built with cutting-edge technology and high-quality materials, ensuring reliable performance and durability. By choosing Zenith’s rock crushers, customers can achieve optimal gravel production with minimal downtime.
Efficiency Analysis: Performance Metrics of Rock Crushers
The efficiency of a rock crusher is determined by several performance metrics, including throughput, reduction ratio, energy consumption, and maintenance requirements. Throughput refers to the amount of material processed by the crusher in a given time period, while the reduction ratio measures the extent to which the material is reduced in size.
Energy consumption is a critical factor in the efficiency of rock crushers, as it directly impacts operational costs. Efficient crushers are designed to minimize energy usage while maximizing output. Maintenance requirements also play a significant role in the overall efficiency, as frequent maintenance can lead to increased downtime and reduced productivity.
Zenith’s rock crushers are engineered to deliver high efficiency and low energy consumption. Our crushers feature advanced technologies such as automated control systems, which optimize the crushing process and reduce energy usage. Additionally, our crushers are designed for easy maintenance, with features such as quick-access service points and durable components, ensuring minimal downtime and maximum productivity.
Environmental Impact: Sustainability of Rock Crushing for Gravel
The environmental impact of rock crushing is a significant consideration in gravel production. The process generates dust, noise, and emissions, which can affect the surrounding environment and communities. Sustainable practices in rock crushing aim to minimize these impacts through the use of advanced technologies and environmentally friendly processes.
Dust suppression systems, such as water sprays and dust collectors, are commonly used to reduce airborne particles during the crushing process. Noise reduction measures, including soundproof enclosures and vibration dampening, help to minimize the impact on nearby communities. Additionally, modern rock crushers are designed to meet stringent emissions standards, reducing their environmental footprint.
Zenith is committed to sustainability in rock crushing. Our crushers are equipped with state-of-the-art dust suppression and noise reduction systems, ensuring compliance with environmental regulations. We also prioritize energy efficiency and emissions reduction in our designs, contributing to a more sustainable gravel production process. By choosing Zenith’s rock crushers, customers can achieve high-quality gravel production while minimizing their environmental impact.
In conclusion, rock crushers are essential for efficient and sustainable gravel production. At Zenith, we offer a wide range of high-performance rock crushers designed to meet the diverse needs of our customers. Our crushers are engineered for maximum efficiency, durability, and environmental sustainability, making them the ideal choice for gravel production. By investing in Zenith’s rock crushers, customers can achieve superior results with reduced operational costs and minimal environmental impact.