Don't miss our holiday offer - 30% OFF!
How Is Sand And Gravel Crushing Equipment Manufactured?
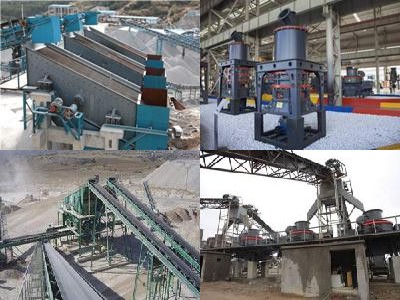
Introduction to Sand and Gravel Crushing Equipment
Sand and gravel crushing equipment is essential in modern construction and mining operations. Primarily used to reduce large rocks, gravel, and sand to more manageable sizes, this equipment comes in various forms, including jaw crushers, cone crushers, impact crushers, and mobile crushers. These machines are designed to handle different capacities and types of materials, ensuring that construction companies can produce the required grades of aggregate efficiently and cost-effectively.
At Zenith, we pride ourselves on our state-of-the-art crushing equipment, which encompasses a variety of machinery designed to meet the needs of diverse projects. Our equipment not only enhances productivity but also delivers superior performance in crushing hard materials such as granite, basalt, and recycled concrete. With continuous advancements in technology, Zenith crushers are now more energy-efficient and environmentally friendly, reducing the overall carbon footprint of our clients.
Understanding the importance of reliable and durable crushing equipment, Zenith offers a comprehensive range of products, including the Zenith PE jaw crusher series, the Zenith HPT cone crusher series, and the Zenith PF impact crusher series. Each of these product lines is tailored to address specific crushing needs, ensuring optimal performance and long service life, which translates to consistent, high-quality output and reduced operational costs for our customers.
Key Manufacturing Processes Involved
The manufacturing of sand and gravel crushing equipment involves several critical processes, each contributing to the final product. The first step is the design phase, where engineers utilize advanced CAD software to create detailed plans for machines that meet industry standards and specific customer requirements. At Zenith, design innovation is at the core of our operations, incorporating feedback from field experiences and integrating the latest technological advancements.
Once the design is finalized, the production phase begins with high-quality materials selection. Premium-grade steel and other alloys are sourced to construct the crushers’ key components, ensuring durability and resistance to wear and tear. Modern fabrication techniques, including CNC machining, laser cutting, and robotic welding, are employed to manufacture the parts with high precision. This meticulous approach guarantees that every component fits perfectly and functions reliably under demanding conditions.
The assembly process is equally crucial, involving skilled technicians who meticulously piece together the machined parts. Quality management systems are adhered to at every stage to ensure each equipment unit meets Zenith’s stringent quality standards. High-precision assembly protocols, coupled with rigorous internal inspections, help us maintain the outstanding reputation of our crushing equipment in the global market.
Quality Control and Testing of Crushing Equipment
Ensuring the reliability and performance of sand and gravel crushing equipment involves comprehensive quality control and testing measures. At Zenith, we implement a multi-tiered quality assurance process, starting from raw material inspection to final product verification. Each material batch undergoes chemical and physical tests to confirm their compliance with manufacturing standards before being utilized in production.
Post-assembly, every piece of crushing equipment is subjected to rigorous testing procedures. These tests simulate real-world operating conditions to evaluate the machine’s performance, durability, and safety. Functional tests and load tests are conducted to ensure that the equipment can handle the specified capacities and material types effectively. Additionally, vibration and noise assessments are carried out to verify that the machines operate within acceptable limits, ensuring a quieter and more efficient performance.
Zenith also places great importance on continuous improvement through customer feedback and field performance monitoring. Our dedicated customer service and support teams work closely with clients to gather insights and address any issues that may arise during operations. This feedback loop helps us fine-tune our manufacturing processes and product designs, maintaining our commitment to delivering the highest quality crushing equipment in the industry.