Don't miss our holiday offer - 30% OFF!
How Much Does A Rock Crusher Cost And Why?
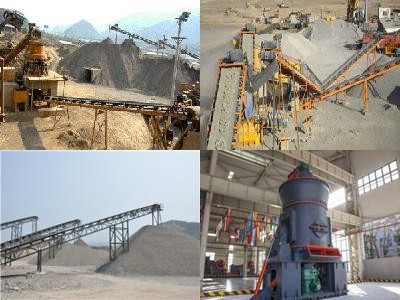
When considering the purchase of a rock crusher, understanding the costs involved and the factors influencing these costs is crucial. At Zenith, we specialize in providing high-quality crushers, mills, and other heavy industrial equipment. This article will delve into the various aspects that determine the cost of a rock crusher, the different types available, the price comparison between new and used crushers, and the hidden costs and maintenance expenses associated with these machines.
Understanding the Factors Influencing Rock Crusher Costs
The cost of a rock crusher is influenced by several factors, including the type of crusher, its capacity, and the materials used in its construction. For instance, crushers made from high-quality steel and equipped with advanced technology tend to be more expensive. Additionally, the capacity of the crusher, which determines how much material it can process in a given time, also plays a significant role in its cost. Larger capacity crushers are generally more expensive due to their ability to handle more material and their increased durability.
Another critical factor is the brand and manufacturer of the crusher. Established brands like Zenith, known for their reliability and advanced technology, often come with a higher price tag. However, investing in a reputable brand can save money in the long run due to lower maintenance costs and longer equipment lifespan. At Zenith, we offer a range of rock crushers designed to meet various needs and budgets, ensuring that our customers get the best value for their investment.
A Breakdown of the Different Types of Rock Crushers
Rock crushers come in various types, each designed for specific applications and materials. The primary types include jaw crushers, cone crushers, impact crushers, and gyratory crushers. Jaw crushers are typically used for primary crushing and are known for their ability to handle large, hard materials. They are often used in mining and construction industries. Cone crushers, on the other hand, are used for secondary crushing and are ideal for crushing medium to hard materials. They offer high efficiency and are commonly used in aggregate production.
Impact crushers are designed for crushing softer materials and are often used in recycling applications. They are known for their ability to produce high-quality, cubical-shaped aggregates. Gyratory crushers are similar to jaw crushers but have a conical head and a concave surface, making them suitable for crushing very hard materials. Each type of crusher has its advantages and is chosen based on the specific requirements of the project. At Zenith, we provide a comprehensive range of crushers to cater to different needs, ensuring optimal performance and efficiency.
Comparing Prices: New vs. Used Rock Crushers
When deciding between a new and a used rock crusher, it’s essential to consider the pros and cons of each option. New rock crushers come with the latest technology and features, ensuring high efficiency and reliability. They also come with warranties and support from the manufacturer, which can be a significant advantage. However, new crushers are generally more expensive, which can be a considerable investment for some businesses.
Used rock crushers, on the other hand, are more affordable and can be a cost-effective solution for businesses with limited budgets. However, they may come with higher maintenance costs and a shorter lifespan compared to new crushers. It’s crucial to thoroughly inspect used equipment and consider the potential costs of repairs and maintenance. At Zenith, we offer both new and used rock crushers, providing our customers with a range of options to suit their needs and budgets.
Hidden Costs and Maintenance Expenses of Rock Crushers
While the initial purchase price of a rock crusher is a significant factor, it’s essential to consider the hidden costs and maintenance expenses associated with owning and operating the equipment. Regular maintenance is crucial to ensure the crusher operates efficiently and has a long lifespan. This includes routine inspections, lubrication, and replacement of worn parts. Neglecting maintenance can lead to costly repairs and downtime, impacting productivity and profitability.
Additionally, the cost of spare parts and consumables, such as liners and wear plates, should be factored into the overall cost of ownership. These parts need to be replaced periodically to maintain the crusher’s performance. At Zenith, we provide comprehensive maintenance services and high-quality spare parts to help our customers minimize downtime and extend the lifespan of their equipment. Investing in regular maintenance and quality parts can significantly reduce the total cost of ownership and ensure the crusher operates at peak efficiency.
Understanding the costs associated with purchasing and operating a rock crusher is essential for making an informed decision. By considering factors such as the type of crusher, capacity, brand, and maintenance expenses, businesses can choose the right equipment to meet their needs. At Zenith, we are committed to providing high-quality crushers and comprehensive support to help our customers achieve optimal performance and efficiency. Whether you are looking for a new or used rock crusher, our team is here to assist you in finding the best solution for your project.