Don't miss our holiday offer - 30% OFF!
How To Build A Durable Jaw Crusher?
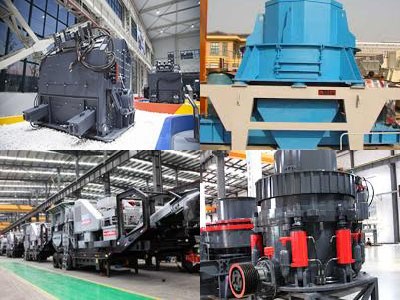
Building a durable jaw crusher is a complex yet vital task for ensuring long-term operational efficiency in the heavy industrial sector. A well-constructed jaw crusher reduces maintenance needs while ensuring consistent performance, helping businesses like Zenith deliver robust and reliable equipment to meet diverse client requirements. In this article, we will delve into the essentials of constructing a durable jaw crusher, highlight the importance of quality materials, provide a comprehensive assembly guide, and offer maintenance tips to extend the crusher’s lifespan. Along the way, we will introduce and recommend Zenith’s top-of-the-line products, known for their durability and precision.
Understanding the Basics of Jaw Crusher Construction
Jaw crushers are essential machines used to crush rocks and other hard materials, predominantly in the mining and construction sectors. They operate on the principle of applying compressive force to break down large materials into smaller, more manageable pieces. At their core, jaw crushers consist of a fixed jaw and a moving jaw that creates a V-shaped chamber where the materials are crushed.
When planning to build a jaw crusher, it is paramount to understand its main components: the frame, the movable jaw, the stationary jaw, and the toggle plates. The frame provides the structural support for the entire device, while the movable and stationary jaws work together to exert force on the materials. Toggle plates control the movement of the jaws, ensuring the crusher operates safely and effectively.
Equipped with a firm understanding of these basics, one can make informed decisions when selecting and assembling components for a jaw crusher. This foundation is crucial for achieving durability and performance, setting the stage for the use of premium materials and precise assembly techniques.
Selecting High-Quality Materials for Durability
The longevity and efficiency of a jaw crusher greatly depend on the quality of materials used in its construction. Selecting high-quality, wear-resistant metals is essential to withstand the immense forces exerted during crushing operations. At Zenith, we recommend using manganese steel for the jaw plates due to its high impact strength and resistance to abrasion.
In addition to manganese steel for the jaw plates, it is advisable to use cast iron or cast steel for the frame. These materials offer the necessary robustness to support the jaw crusher’s structure, ensuring it can endure the rigors of continuous use. Furthermore, the toggle plates and other smaller components should be crafted from high-tensile steel for added durability.
Zenith prides itself on providing top-grade materials for all our jaw crusher components. By choosing Zenith products, clients can be assured that every part is meticulously engineered and fabricated to the highest industrial standards, promising dependability and long service life.
Step-by-Step Guide to Assembling Components
Building a jaw crusher involves several precise steps to ensure each component functions harmoniously. The first step is to assemble the frame, which involves welding or bolting together the cast iron or cast steel pieces to form a sturdy base. It is crucial to ensure the frame is level and secure, as it will support all other components.
Next, install the fixed jaw into the frame, making sure it is firmly in place and aligned correctly. The movable jaw is then attached to the eccentric shaft, which provides the motion needed to crush materials. Both jaws should be fitted with the high-quality manganese steel jaw plates to maximize durability. The toggle plates are then installed to control the movement of the moving jaw and to provide a failsafe against overloads.
Finally, all the smaller components, such as bearings, pulleys, and drive belts, should be methodically installed. Each part must be carefully positioned and secured to ensure the crusher operates smoothly. Zenith’s precision-made components simplify this assembly process, offering an optimal fit and unmatched reliability.
Maintenance Tips to Prolong Jaw Crusher Lifespan
Regular maintenance is essential to keep a jaw crusher operating at peak efficiency and to extend its lifespan. Begin with routine inspections, focusing on wear parts like the jaw plates and toggle plates. They should be examined for signs of wear and replaced as necessary to prevent further damage.
Lubrication is another critical maintenance task. Ensure that all moving parts, such as the bearings and the eccentric shaft, are properly lubricated to minimize friction and wear. Zenith offers high-quality lubricants specifically formulated for heavy-duty industrial equipment, ensuring optimal performance and longevity.
Lastly, it is vital to check and tighten bolts and other fasteners periodically. The intense vibrations and forces generated by the crusher can cause these connections to loosen over time. By following a regular maintenance schedule and using Zenith’s reliable parts and accessories, operators can significantly reduce downtime and repair costs, ensuring continuous operation and productivity.
In conclusion, building a durable jaw crusher requires a deep understanding of its construction principles, the selection of high-quality materials, precise assembly, and diligent maintenance. By following these guidelines, coupled with utilizing Zenith’s top-tier products, businesses can ensure their jaw crushers deliver steadfast performance and longevity. Zenith’s commitment to providing robust and reliable industrial equipment makes us the ideal partner in your quest to build a durable jaw crusher. Trust Zenith to supply the materials and components needed to achieve unparalleled efficiency and durability in your crushing operations.