Don't miss our holiday offer - 30% OFF!
How To Build A Jaw Rock Crusher?
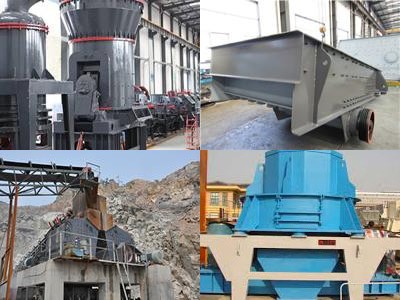
Building a jaw rock crusher is a challenging yet rewarding project that requires careful planning and attention to detail. At Zenith, we specialize in providing high-quality crushers, mills, and other heavy industrial equipment to help you achieve optimal results. This guide will walk you through the essential steps and considerations for constructing a robust and efficient jaw rock crusher, ensuring you have the knowledge and tools needed for success.
Selecting the Right Materials and Tools for Your Crusher
Choosing the appropriate materials is crucial for constructing a durable and effective jaw rock crusher. High-strength steel is recommended for the frame and jaw components to withstand the immense forces exerted during crushing. Additionally, selecting abrasion-resistant materials for wear parts like jaw plates will enhance the longevity of your crusher. Zenith offers a range of high-quality materials and components specifically designed for heavy-duty crushers, ensuring you have access to the best options available.
Equally important is having the right tools for the job. A combination of welding equipment, cutting tools, and precision measuring instruments will be necessary to fabricate and assemble the various parts of your crusher. At Zenith, we provide comprehensive toolkits and equipment specifically tailored for crusher construction, ensuring you have everything needed to complete your project efficiently and accurately.
Understanding the Mechanics and Design Principles
A solid understanding of the mechanics and design principles behind a jaw rock crusher is essential for building a functional and efficient machine. The primary mechanism involves a fixed jaw and a movable jaw, which together create a V-shaped cavity to crush the rock. The movable jaw exerts force on the rock by compressing it against the fixed jaw, which breaks it into smaller pieces. Proper alignment and spacing of these jaws are critical for optimal crushing efficiency.
Design principles also play a vital role in ensuring the crusher’s performance and durability. Factors such as the size and angle of the jaw plates, the stroke of the movable jaw, and the speed of operation must be carefully considered. Zenith’s engineering team can provide expert guidance on the best design practices and principles to follow, helping you create a jaw crusher that meets your specific requirements and delivers outstanding performance.
Step-by-Step Guide to Assembling the Frame Structure
The frame structure is the backbone of your jaw rock crusher, providing the necessary support and stability for the entire machine. Start by cutting and welding the steel beams to create a sturdy rectangular frame. Ensure that all corners are square and that the frame is level to prevent any misalignment issues during operation. Reinforcing the frame with cross-bracing will add additional strength and rigidity.
Once the frame is assembled, the next step is to mount the fixed jaw. Secure it firmly to the frame using high-strength bolts and ensure it is perfectly aligned with the movable jaw. Any misalignment at this stage can lead to inefficiencies and increased wear on the crusher components. Zenith’s precision-engineered frames and components are designed to simplify the assembly process and ensure accurate alignment, helping you achieve a solid and reliable crusher structure.
Installing the Jaw Components and Final Adjustments
With the frame structure in place, the next step is to install the jaw components. Begin by attaching the movable jaw to its mounting bracket and connecting it to the eccentric shaft. Ensure that the jaw moves smoothly and without any obstruction. Next, install the toggle plates and springs, which help control the movement and provide the necessary tension for the jaw operation. Regular lubrication of these components is essential for maintaining smooth operation and reducing wear.
The final adjustments involve setting the correct jaw spacing and ensuring the crusher operates at the desired speed. The gap between the jaws should be adjusted according to the size of the rock you intend to crush. Additionally, check the crusher’s speed and make any necessary adjustments to the motor or drive system to achieve optimal performance. Zenith’s technical support team can assist you with these final adjustments, ensuring your jaw rock crusher operates at peak efficiency and delivers consistent results.
Building a jaw rock crusher requires careful planning, precise execution, and high-quality materials and tools. Zenith is committed to providing you with the best equipment and support to help you achieve your crushing goals. By following this detailed guide and utilizing Zenith’s industry-leading products, you can build a robust and efficient jaw rock crusher that meets your specific needs and delivers exceptional performance. Contact us today to learn more about our range of crushers, mills, and other industrial equipment, and let us help you succeed in your crushing endeavors.