Don't miss our holiday offer - 30% OFF!
How To Determine The Right Size For A Gyratory Crusher?
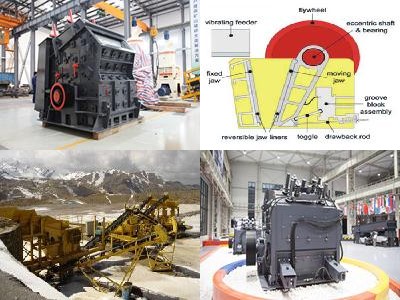
Selecting the right size for a gyratory crusher is critical for achieving optimal performance in mining and aggregate operations. Choosing the correct crusher size ensures efficient material processing, maximizes productivity, and reduces operational costs. At Zenith, we specialize in providing high-quality crushers, mills, and other heavy industrial equipment to meet the diverse needs of our clients. This article will guide you through the essential factors to consider when determining the right size for a gyratory crusher.
Understanding Gyratory Crushers and Their Applications
Gyratory crushers are a type of primary crusher used extensively in the mining and aggregate industries. They function by compressing feed material between a stationary concave surface and a moving mantle. This crushing action is highly effective for breaking down large, hard materials into smaller, more manageable pieces. Gyratory crushers are ideal for handling high-capacity operations and can process a wide range of materials, from soft to very hard rocks.
The primary application of gyratory crushers lies in their ability to handle high throughput rates. This makes them particularly suitable for large-scale mining operations where the volume of material to be processed is substantial. Additionally, their robust design and construction allow them to operate continuously under harsh conditions, ensuring reliable performance and longevity.
At Zenith, our range of gyratory crushers is designed to cater to various industrial needs. Our crushers are engineered to deliver superior performance, reliability, and efficiency. With advanced features and innovative technology, Zenith gyratory crushers provide the ideal solution for your crushing requirements.
Key Factors Influencing Crusher Size Selection
Several critical factors must be considered when selecting the appropriate size of a gyratory crusher. One of the primary considerations is the feed size of the material to be processed. The crusher must be capable of handling the largest pieces of material that will be fed into it. This ensures that the crusher can efficiently process the material without causing blockages or interruptions.
Another essential factor is the capacity requirements of the operation. The chosen crusher must be able to handle the desired throughput rate, ensuring that the processing plant operates at optimal efficiency. This involves calculating the expected production rates and matching them with the crusher’s capacity to ensure seamless operation.
The final consideration is the desired product size. The crusher’s settings and design must allow for the production of the required output size. This involves adjusting the crusher’s parameters to achieve the desired reduction ratio and ensuring that the final product meets the specifications for downstream processing.
Analyzing Material Characteristics for Optimal Fit
Understanding the characteristics of the material to be processed is crucial for selecting the right size gyratory crusher. Different materials have varying properties, such as hardness, abrasiveness, and moisture content, which can significantly impact the crusher’s performance. Analyzing these properties helps in choosing a crusher that can handle the material efficiently and effectively.
Hardness is a critical factor to consider. Materials with high hardness levels require crushers with robust construction and powerful crushing mechanisms to break them down. On the other hand, softer materials can be processed with crushers that have less aggressive crushing actions. Zenith gyratory crushers are designed to accommodate a wide range of material hardness, ensuring optimal performance across different applications.
Abrasiveness is another important characteristic. Materials that are highly abrasive can cause significant wear and tear on the crusher’s components. It is essential to select a crusher with durable wear parts and a design that minimizes wear to ensure longevity and reduce maintenance costs. Zenith’s crushers are built with high-quality materials and advanced engineering to withstand abrasive conditions.
Lastly, the moisture content of the material can affect the crusher’s performance. High moisture levels can cause clogging and reduce the efficiency of the crushing process. Selecting a crusher that can handle materials with varying moisture levels ensures consistent performance and prevents operational issues.
Calculating Capacity and Output Requirements
To determine the right size for a gyratory crusher, it is essential to calculate the capacity and output requirements of the operation. This involves assessing the expected production rates and matching them with the crusher’s capacity to ensure efficient and seamless operation. Factors such as the daily production targets, the duration of operation, and the desired final product size must be considered.
The capacity of a gyratory crusher is typically measured in tons per hour (tph). It is important to choose a crusher that can handle the peak production rates without compromising performance. This involves understanding the material’s density, the feed size, and the desired product size to accurately calculate the required capacity. Zenith’s gyratory crushers are available in various sizes and capacities to meet the specific needs of different operations.
In addition to capacity, the output requirements must also be considered. The crusher must produce the desired product size consistently and efficiently. This involves adjusting the crusher’s settings and design to achieve the required reduction ratio and ensure that the final product meets the specifications for downstream processing. Zenith’s crushers are designed with advanced features that allow for precise control over the output size, ensuring consistent and high-quality results.
Lastly, it is important to consider future expansion plans and potential changes in production requirements. Selecting a crusher with a higher capacity than currently needed can provide flexibility for future growth and changes in production demands. Zenith offers a range of crushers with scalable capacities to accommodate the evolving needs of your operation.
Determining the right size for a gyratory crusher is a crucial step in ensuring the efficiency and productivity of your mining or aggregate operation. By understanding the key factors influencing crusher size selection, analyzing material characteristics, and accurately calculating capacity and output requirements, you can make an informed decision that will benefit your operation in the long run. Zenith is committed to providing high-quality crushers, mills, and other heavy industrial equipment to meet your specific needs. Our range of gyratory crushers offers superior performance, reliability, and efficiency, making them the ideal choice for your crushing requirements.