Don't miss our holiday offer - 30% OFF!
How To Maintain And Replace Cone Crusher Parts Effectively?
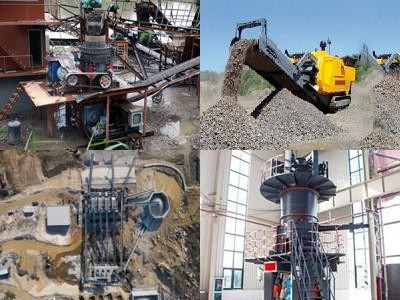
Maintaining and replacing cone crusher parts is vital to the efficiency and longevity of the crusher. Without proper maintenance, the crusher can face unexpected downtime, which can adversely impact production and profitability. At Zenith, we have extensive experience in manufacturing superior crushers, mills, and other heavy industrial equipment. Our products, including high-quality cone crusher parts, are designed to enhance performance and durability. This guide provides detailed insights into maintaining and replacing cone crusher parts effectively to ensure optimal functioning and longevity of your equipment.
Understanding Cone Crusher Mechanisms and Components
Cone crushers are intricate machines designed to reduce large rocks into finer materials. They work by employing a rotating mantle within a concave bowl to crush the material within an adjustable gap. The key components include the feed hopper, which funnels the raw material into the crushing chamber, and the mantle and concave, which are the primary wearing components. Other significant parts include the eccentric shaft, which allows the mantle to gyrate, and the drive system, which powers the entire operation.
Knowing how a cone crusher operates is essential for maintaining its efficiency. The crushing action takes place through a combination of compression and shearing, which exerts high levels of force on the materials. This continuous high-pressure environment demands robust and durable materials for the crusher components. At Zenith, our cone crusher parts are crafted with precision, ensuring they can withstand rigorous conditions and provide extended service life.
The adjustability of the cone crusher allows operators to modify the discharge size to meet specific requirements. This involves changing the gap between the mantle and the concave, which can be done remotely on modern models. Understanding these mechanisms and components enables operators to optimize operational efficiencies and maintain consistent product quality, ensuring the crusher performs at its best.
Essential Maintenance Practices for Cone Crushers
Effective maintenance for cone crushers involves a combination of preventive measures and regular inspections. First and foremost, lubrication is vital. Ensuring that all moving parts are adequately lubricated reduces friction and wear, preventing premature failure. Using high-quality lubricants, such as those recommended by Zenith, can significantly enhance the lifespan of the machine.
Regular inspections are another critical aspect of cone crusher maintenance. By frequently checking the wear levels of the mantles, concaves, and other critical components, operators can predict when replacements are necessary, preventing unexpected breakdowns. Scheduled downtime for thorough inspections should be integrated into the maintenance routine to address minor issues before they escalate into major problems.
Additionally, keeping the crushing area clean and removing obstructions from the feed hopper can prevent blockages that could damage components. Ensuring that the feed is consistently regulated to avoid overloading the crusher is also essential. Zenith’s range of maintenance products and tools can assist in these practices, ensuring you maintain a high level of productivity while minimizing downtime.
Identifying Signs of Wear in Cone Crusher Parts
Recognizing the early signs of wear in cone crusher parts can save significant time and cost by addressing issues before they lead to equipment failure. One of the most common signs of wear is a decrease in crusher performance, including reduced efficiency and a less uniform output size. Monitoring these performance indicators can provide early warnings that parts may need inspection or replacement.
Visible wear and tear on the mantle and concave are also clear indicators. As these parts are subject to constant abrasion, they will exhibit wear patterns that can be seen during regular inspections. Wear can manifest as grooves, scratches, or even cracks on the surface. Using Zenith’s high-quality, wear-resistant components can extend the interval between necessary replacements.
Another subtle yet crucial sign is unusual noises coming from the crusher. Grinding, banging, or popping sounds can indicate that parts are either excessively worn or not aligned correctly. It is crucial to address these sounds immediately by inspecting the potential source of the issue. Regular training on wear patterns and using testing equipment can greatly assist in identifying these issues early on.
Step-by-Step Guide to Replacing Worn Crusher Parts
Replacing worn cone crusher parts can be a detailed process, but it is essential for maintaining optimal performance and avoiding unscheduled downtime. The first step is to organize all the required tools and replacement parts. Zenith offers comprehensive replacement kits and tools, ensuring that you have everything you need for the replacement process.
Start by safely shutting down the crusher and ensuring that it cannot be accidentally restarted. Remove the worn parts carefully, beginning with the mantle, and then proceed to the concave. During this process, it is crucial to keep the work area clean and organized to prevent any small parts from getting lost or damaged. Cleaning the area where the parts are removed from will help in installing the new parts more effectively.
The installation of new parts should be done meticulously, ensuring they fit correctly and are properly aligned. Carefully follow the manufacturer’s guidelines to torque bolts to the specified values. After installation, perform a thorough check to ensure all parts are secure. Once the crusher is restarted, allow it to run for a short period to ensure everything is functioning correctly and listen for any unusual noises. Zenith’s after-sales support team can provide guidance and assistance during this process, ensuring a smooth and successful replacement.
Proper maintenance and timely replacement of cone crusher parts are essential for the longevity and performance of the crusher. By understanding the mechanisms involved, adhering to maintenance best practices, identifying wear signs early, and meticulously replacing parts, operators can avoid unexpected downtime and maintain high efficiency. At Zenith, we pride ourselves on offering top-tier cone crusher parts and comprehensive support to ensure your equipment operates at peak performance. Trust Zenith to keep your crushers running smoothly and efficiently, maximizing your productivity and profitability.