Don't miss our holiday offer - 30% OFF!
Unlocking Efficiency: Exploring The Capacity Of Jaw Crushers
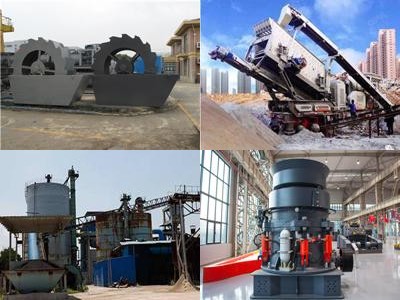
Jaw crushers stand as stalwarts in both the mining and construction industries, serving as essential workhorses in the crushing of various materials. As primary crushers, they play a pivotal role in reducing the size of rocks, ores, and other aggregates for further processing. This article aims to explore a crucial aspect of jaw crushers: their capacity. By delving into the factors influencing capacity, strategies for maximizing efficiency, and real-world case studies, we aim to provide valuable insights for professionals seeking to optimize their crushing operations.
Introduction to Jaw Crushers
Jaw crushers, fundamental to material processing operations, consist of a fixed jaw and a movable jaw, with the material being crushed between them. These robust machines employ mechanical pressure to break down even the toughest materials. The fixed jaw remains stationary, while the movable jaw exerts force, creating a crushing action. This mechanical process efficiently reduces large rocks into smaller, more manageable sizes, making them suitable for subsequent processing stages.
Factors Influencing Capacity
The capacity of a jaw crusher is influenced by several key factors that must be carefully considered to optimize performance. One such factor is the feed size, which directly impacts the crusher’s ability to process materials efficiently. Additionally, the closed side setting, or the smallest distance between the jaw plates at the bottom of the crushing chamber, plays a critical role in determining the crusher’s capacity. Material characteristics, such as hardness, abrasiveness, and moisture content, further influence capacity and must be taken into account during operation.
Maximizing Efficiency
To maximize the efficiency of jaw crushers, various strategies can be employed. Regular maintenance routines, including lubrication, inspection of wear parts, and tightening of loose components, are essential for ensuring optimal performance and prolonging equipment lifespan. Furthermore, operational techniques, such as adjusting the closed side setting and controlling the feed rate, can help achieve higher throughput and improved overall efficiency.
Case Studies and Applications
Real-world case studies offer valuable insights into the practical application of capacity optimization strategies for jaw crushers. By examining successful implementations in diverse mining and construction scenarios, professionals can glean actionable recommendations for their own operations. From increasing throughput in hard rock mining applications to achieving finer particle sizes in aggregate production, these case studies demonstrate the versatility and effectiveness of optimizing jaw crusher capacity.
In conclusion, unlocking the full capacity of jaw crushers is imperative for achieving optimal efficiency and productivity in material processing operations. By understanding the factors influencing capacity and implementing effective strategies for optimization, professionals can elevate their crushing operations to new heights of performance. At Zenith, we offer a range of high-quality jaw crushers and complementary equipment designed to enhance crushing efficiency and maximize throughput. Explore our selection of crushers, mills, and other heavy industrial equipment to elevate your operations and unlock greater productivity.