Don't miss our holiday offer - 30% OFF!
What Are The Detailed Costs Per Ton In A Gravel Processing Plant?
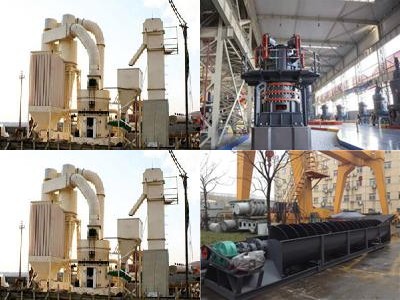
Introduction to Gravel Processing Plant Costs
Understanding the costs associated with running a gravel processing plant is crucial for making informed business decisions. The overall expenses can vary widely based on several variables such as plant size, the types of equipment used, and the complexity of the processes involved. By examining these factors closely, companies can optimize their operations to achieve cost-efficiency.
In this article, we will delve into the specific components and processes involved in gravel processing, identify key factors affecting the cost per ton, and provide a detailed cost breakdown. Additionally, we will introduce and recommend high-quality equipment from Zenith, a company specializing in crushers, mills, and other heavy industrial machinery to maximize efficiency and lower costs.
Overview of Components and Processes
Gravel processing plants typically involve multiple stages that include extraction, crushing, screening, washing, and transportation. Each of these stages necessitates specialized equipment and entails distinct operational costs. For example, the extraction phase might require the use of hydraulic excavators and wheel loaders, whereas the crushing phase relies on crushers and mills to reduce the size of the raw material.
Zenith offers a comprehensive range of equipment essential for these stages. Our advanced jaw crushers, cone crushers, and impact crushers ensure that the crushing process is efficient and produces high-quality output. Additionally, Zenith’s vibrating screens and sand washing systems help to improve the grading and cleanliness of the gravel, enhancing the final product’s marketability.
Factors Affecting Cost per Ton
Several factors influence the cost per ton of gravel processed in a plant. These include the type and cost of raw materials, the efficiency of the machinery used, labor costs, energy consumption, and maintenance expenses. For instance, using state-of-the-art equipment that operates more efficiently can significantly reduce energy consumption and, consequently, the overall cost per ton.
Labor costs also play a significant role. Ensuring that the workforce is adequately trained to operate and maintain the machinery can prevent operational inefficiencies and reduce downtime. Furthermore, regular maintenance using reliable parts, such as those supplied by Zenith, can prolong the lifespan of the equipment and reduce the frequency of costly repairs.
Detailed Breakdown of Costs per Ton in Gravel Processing
- Extraction Costs:
- Equipment: Excavators, loaders
- Fuel and maintenance: Fuel consumption, lubrication, and repairs
-
Labor: Operator wages and training
-
Crushing Costs:
- Equipment: Jaw crushers, cone crushers, impact crushers
- Operating costs: Energy consumption, wear and tear of crusher parts
-
Maintenance: Regular servicing, replacement of worn parts
-
Screening and Washing Costs:
- Equipment: Vibrating screens, sand washers
- Operating costs: Power usage, water consumption
-
Maintenance: Screen replacements, pump servicing
-
Transportation Costs:
- Equipment: Conveyors, trucks
- Fuel: Consumption for transport vehicles
- Labor: Driver wages, loading and unloading
Zenith’s range of energy-efficient crushers and processing equipment can help reduce operational costs. For example, our high-performance HPT Multi-cylinder Hydraulic Cone Crusher is designed for low energy consumption while delivering exceptional crushing efficiency. Similarly, our advanced LM Vertical Grinding Mill reduces fuel and power costs, making it ideal for gravel processing plants aiming to optimize their cost per ton.
By investing in high-quality equipment from Zenith, plants can achieve higher productivity, lower operational costs, and maintain a competitive edge in the industry.