Don't miss our holiday offer - 30% OFF!
What Are The Different Types Of Crusher Machines Available Today?
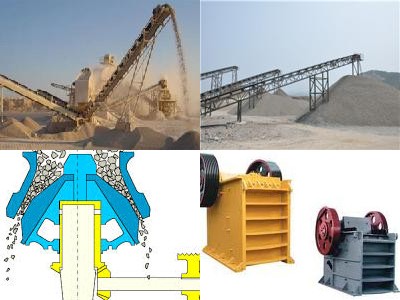
Crusher machines play a crucial role in the mining and construction industries, facilitating the reduction of large rocks, ores, and other materials into manageable sizes. As a leading provider of heavy industrial equipment, Zenith is committed to offering innovative and efficient crusher solutions to meet diverse industry needs. This article explores the different types of crusher machines available today, highlighting their functionalities and recommending Zenith’s high-quality products.
Understanding the Various Crusher Machine Types
Crusher machines are essential in the crushing and mining industries, with various types designed to handle different materials and applications. The primary categories include primary crushers, secondary crushers, and tertiary crushers. Each type serves a specific purpose and is engineered to deliver optimal performance in its designated area of application.
At Zenith, we offer a comprehensive range of crusher machines tailored to meet the unique requirements of our customers. Our portfolio includes jaw crushers, gyratory crushers, cone crushers, and impact crushers, each designed with cutting-edge technology and robust construction to ensure durability and efficiency. Understanding the distinct features and benefits of each type can help businesses make informed decisions about their crushing needs.
In this article, we will delve into the specifics of primary crushers such as jaw and gyratory crushers, followed by an exploration of secondary and tertiary crushers, including cone and impact crushers. By the end of this read, you will have a clear understanding of the various crusher machines available and how Zenith’s products can enhance your operational efficiency.
Primary Crushers: Jaw and Gyratory Crushers Explained
Primary crushers are the first stage in the crushing process, tasked with reducing large rocks and ores into smaller, more manageable sizes. Jaw crushers and gyratory crushers are the most common types of primary crushers, each offering unique advantages for different applications.
Jaw crushers are characterized by their simple design and robust construction, making them ideal for heavy-duty crushing tasks. These machines use compressive force to break down materials, with a stationary jaw and a movable jaw working together to crush the material. Zenith’s jaw crushers are engineered for high performance, with models like the PE series offering exceptional efficiency and durability for various crushing operations.
Gyratory crushers operate on a similar principle but are designed for higher capacity and continuous operation. They feature a concave surface and a conical head, with the material being crushed between the two surfaces. Gyratory crushers are well-suited for large-scale mining and quarrying operations, where high throughput and consistent product size are essential. Zenith’s gyratory crushers boast superior design and construction, ensuring reliable performance and minimal downtime.
In conclusion, primary crushers are integral to the initial stages of material processing, with jaw and gyratory crushers being the most prevalent types. Zenith’s range of primary crushers is designed to deliver excellent performance, reliability, and efficiency, making them a valuable addition to any crushing operation.
Secondary and Tertiary Crushers: Cone, Impact, and More
Secondary and tertiary crushers are employed after primary crushers to further reduce material size and shape, ensuring the final product meets specific requirements. These stages often involve cone crushers, impact crushers, and other specialized machines designed for precise crushing.
Cone crushers are widely used in secondary and tertiary crushing stages due to their versatility and efficiency. They operate on the principle of an oscillating shaft, with the material being compressed between a fixed outer mantle and a moving inner cone. Zenith’s cone crushers, such as the HPT series, are renowned for their high performance, advanced technology, and excellent product quality, making them ideal for a variety of applications.
Impact crushers are another popular choice for secondary and tertiary crushing, particularly when a high reduction ratio and a more cubical product shape are desired. These crushers use impact force to break down materials, with a high-speed rotor and anvils or blow bars. Zenith’s impact crushers, including the CI5X series, are designed for maximum efficiency and durability, offering superior performance in both primary and secondary crushing applications.
In addition to cone and impact crushers, other specialized machines like roll crushers and hammer mills can also be used for secondary and tertiary crushing. Each type offers distinct advantages, depending on the material and desired output. Zenith provides a wide range of options, ensuring that our customers can find the perfect crusher to meet their specific needs.
In summary, understanding the different types of crusher machines available today is crucial for optimizing the crushing process and achieving desired results. From primary crushers like jaw and gyratory crushers to secondary and tertiary crushers such as cone and impact crushers, each type serves a unique purpose in the material reduction process. As a leading provider of heavy industrial equipment, Zenith offers a comprehensive range of crusher machines designed to deliver exceptional performance, reliability, and efficiency. By choosing Zenith’s high-quality products, businesses can enhance their operational efficiency and achieve their crushing goals with confidence.