Don't miss our holiday offer - 30% OFF!
What Are The Different Types Of Crushers Used In Mineral Processing?
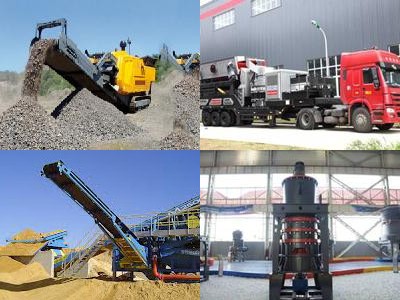
Crushers are essential in the mineral processing industry, used to reduce the size of raw materials for further processing. Understanding the different types of crushers and their specific applications is crucial for selecting the right equipment for your needs. At Zenith, we offer a variety of crushers designed for different stages of the mineral processing workflow. This article will delve into the primary, secondary, and tertiary crushers, explaining their roles and highlighting our top-quality products that can help enhance your processing operations.
Understanding Primary Crushers in Mineral Processing
Primary crushers are the first stage of material reduction in mineral processing. They are designed to handle large, coarse materials directly from the mining site. These crushers are typically robust and capable of handling hard and abrasive rocks. The primary crusher’s main goal is to reduce the size of the raw material to a manageable level for secondary crushers. Types of primary crushers include jaw crushers, gyratory crushers, and impact crushers.
Jaw crushers are one of the most commonly used primary crushers. They operate by compressing the material between a stationary plate and a moving plate. This action crushes the material to the desired size. Zenith’s jaw crushers are known for their durability and efficiency, making them an excellent choice for primary crushing needs.
Gyratory crushers are another type of primary crusher, designed to handle large rocks and ores. They work on a similar principle to jaw crushers but with a gyrating spindle that crushes the material against a fixed outer wall. Zenith’s gyratory crushers offer high capacity and are ideal for processing large quantities of material in a single pass.
Exploring Secondary Crushers and Their Functions
Secondary crushers take the output from primary crushers and further reduce the size of the material. These crushers are essential for producing the finer material required for subsequent processing stages. Secondary crushers come in various types, including cone crushers, hammer mills, and impact crushers.
Cone crushers are prevalent in secondary crushing. They operate by crushing the material between a rotating cone and a fixed outer wall. This type of crusher is known for its ability to produce uniform-sized particles, making it ideal for producing high-quality aggregate. Zenith’s cone crushers are designed with advanced technology to ensure high performance and reliability.
Hammer mills are another type of secondary crusher, utilizing rotating hammers to crush the material. They are highly effective for materials that are not too hard and can be reduced to a fine size. Zenith’s hammer mills are built to last, offering efficient and consistent performance in secondary crushing applications.
Impact crushers in secondary crushing use high-speed impact force to break down materials. These crushers are suitable for materials that are softer and less abrasive. Zenith’s impact crushers are engineered to deliver high reduction ratios and excellent product shape, making them a valuable addition to any mineral processing operation.
Tertiary Crushers: Enhancing the Mineral Processing Stage
Tertiary crushers are used for the final stage of crushing, producing the finest material required for various applications. These crushers are often used in combination with secondary crushers to achieve the desired product size and shape. Types of tertiary crushers include roll crushers, vertical shaft impactors (VSI), and high-pressure grinding rolls (HPGR).
Roll crushers are effective tertiary crushers that use compression to crush the material between two rotating cylinders. They are well-suited for producing fine materials with minimal fines generation. Zenith’s roll crushers are designed for precision and efficiency, ensuring optimal performance in tertiary crushing.
Vertical shaft impactors (VSI) are another type of tertiary crusher, using a high-speed rotor to throw the material against a hard surface, causing it to break apart. This method produces well-shaped particles and is ideal for applications requiring high-quality sand and gravel. Zenith’s VSI crushers are engineered for maximum efficiency and longevity, providing excellent value for mineral processing operations.
High-pressure grinding rolls (HPGR) are advanced tertiary crushers that use high pressure to crush the material between two counter-rotating rolls. This method is highly efficient and can produce very fine material with minimal energy consumption. Zenith’s HPGR crushers are designed to handle the toughest materials, delivering superior performance in tertiary crushing.
Choosing the right type of crusher is crucial for optimizing your mineral processing operations. At Zenith, we offer a comprehensive range of crushers designed to meet the specific needs of each stage of the crushing process. From robust primary crushers to efficient secondary and precise tertiary crushers, our equipment is built to deliver exceptional performance and reliability. Trust Zenith for all your crushing needs, and let us help you achieve your mineral processing goals with our top-of-the-line products.