Don't miss our holiday offer - 30% OFF!
What Determines The Capacity Of A Cone Crusher?
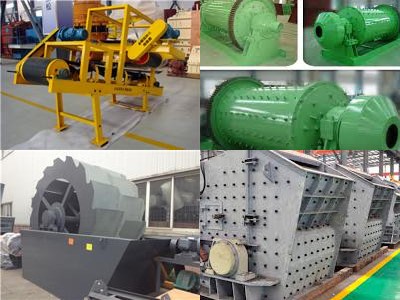
Cone crushers are integral parts of the crushing process in many industries, including mining, quarrying, and recycling. At Zenith, we specialize in high-quality crushers, mills, and heavy industrial equipment designed to maximize efficiency and productivity. In this article, we delve into the various factors that determine the capacity of a cone crusher, examining material properties, design considerations, and technical specifications. Understanding these elements can help you make an informed decision when selecting the right cone crusher for your operations.
Factors Influencing Cone Crusher Capacity
The capacity of a cone crusher is determined by several factors, the most significant of which include the operational parameters such as the close side setting (CSS), the open side setting (OSS), feed size distribution, and the speed at which the crusher operates. A tighter close side setting can lead to a finer product but may also reduce throughput, whereas a wider open side setting can enhance production but potentially at the cost of product granularity. Feed size distribution is equally crucial – uneven or oversized feed can cause blockages and reduce efficiency. Crusher speed also plays a vital role; increasing speed can boost production capacity but might result in excessive wear and tear on the machine.
Another critical aspect is the crushing chamber design. The chamber must be appropriately configured to facilitate an optimal balance between larger and smaller grains to ensure efficient processing. Chamber size and shape, liner profiles, and the material used for liners directly impact the crushing capacity. For example, concave and mantle shapes help determine the crushing action and subsequent capacity. At Zenith, our cone crushers are designed with robust chambers that maximize crushing efficiency and throughput, ensuring that our customers achieve the best possible outcomes for their specific needs.
Material Properties and Their Impact on Crushing
The properties of the material being processed significantly affect the capacity of a cone crusher. Hardness, abrasiveness, moisture content, and bulk density of the feed material can all influence the machine’s performance. Hard, brittle materials usually result in slower crushing processes and reduced capacities, whereas softer, less abrasive materials allow for higher throughput rates. Moisture content, particularly, can pose challenges, as high moisture levels can lead to clogging within the crushing chamber, reducing capacity and potentially damaging the crusher.
Material bulk density and particle size distribution also play crucial roles in determining the machine’s capacity. Materials with a high bulk density allow for higher throughput while those with heterogeneous particle sizes require more energy to crush, thereby decreasing capacity. Ensuring a homogeneous feed material can significantly enhance the performance of a cone crusher. Zenith crushers are designed to handle a diverse range of materials efficiently. Our advanced engineering ensures that our equipment can process various material types while maintaining high productivity levels.
Design and Technical Specifications of Cone Crushers
The design and technical specifications of cone crushers significantly influence their capacity. Key design features, such as the size and shape of the feed opening, the angle of the cone, and the speed of rotation, are critical considerations. A wider feed opening allows a higher volume of material to enter the crusher, facilitating increased throughput. The cone angle determines the sufficient levels of compression and the uniformity of the final product. Additionally, the rotational speed dictates the frequency of crushing cycles, directly impacting capacity.
Technical specifications such as power rating, hydraulic systems, and automation features also determine crushing capacity. Higher power ratings enable crushers to process tougher materials more efficiently. Modern hydraulic systems are used to adjust crusher settings automatically, optimizing performance and preventing overloading. Furthermore, automation features enhance operational efficiency by providing real-time data and diagnostics to adjust settings and ensure consistent crusher performance. Zenith’s cone crushers incorporate cutting-edge technology and robust design, resulting in optimal performance and high productivity for our clients.
In conclusion, the capacity of a cone crusher hinges on a range of factors, including operational parameters, material properties, and design specifications. Understanding these intricacies allows for optimized crusher selection and usage, maximizing efficiency and productivity. At Zenith, we pride ourselves on offering top-of-the-line cone crushers engineered for high performance and durability. Our crushers are designed to handle diverse materials and demanding conditions, ensuring that our customers achieve superior results in their crushing operations. Trust Zenith for all your crushing and milling needs, and experience the unparalleled performance of our state-of-the-art equipment.