Don't miss our holiday offer - 30% OFF!
What Is The Typical Process Flow Of A Crushing Plant?
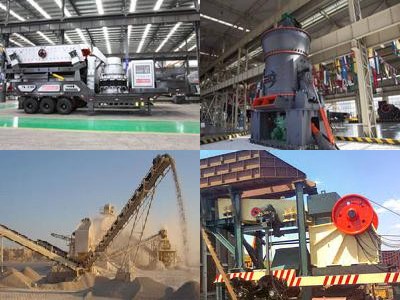
In the world of mining and aggregate processing, a well-designed crushing plant is essential for the efficient operation and production of high-quality materials. Zenith company, a leader in manufacturing crushers, mills, and other heavy industrial equipment, provides cutting-edge solutions to optimize every stage of the crushing process. In this article, we will detail the typical process flow of a crushing plant, from primary crushing all the way to tertiary crushing and screening, highlighting how Zenith products can enhance each stage.
Overview of the Crushing Plant Process Flow
The crushing plant’s process flow is meticulously designed to convert large raw materials into smaller, more manageable sizes for further processing. This multi-stage operation involves several layers of reduction, screening, and refinement to achieve the desired product quality and specifications. Typically, the process begins with large chunks of raw materials being fed into primary crushers, followed by secondary and tertiary crushing stages, where size reduction and shape refinement are carried out systematically.
Understanding the flow of the entire crushing process is crucial for operators to ensure optimal performance and efficiency. At Zenith, we offer comprehensive solutions that map out every step of the process, providing both the machinery and the expertise needed to fine-tune the operations. Our cutting-edge technology ensures seamless integration of each stage, resulting in consistent and high-quality output.
Each component of the plant, from the feeding system to the final screening stage, works in unison to deliver precision and efficiency. Zenith’s expertise in this domain allows us to design custom solutions that meet specific production needs, ensuring that every plant operates at its best.
Primary Crushing: Initial Size Reduction Stage
Primary crushing is the first stage in the crushing process where large rocks from the quarry are fed into the primary crusher to be reduced in size. This stage is critical as it sets the foundation for all subsequent steps. The primary crusher is designed to handle the largest pieces of raw material, breaking them down to manageable sizes for further processing.
Zenith offers a range of primary crushers, including jaw crushers and gyratory crushers, each engineered to handle varying materials and capacities. Our jaw crushers, known for their durability and efficiency, are ideal for large-scale operations. They utilize compressive force to break down large rocks, making them suitable for the initial stage of the crushing process.
Ensuring reliable performance at this stage is vital. Zenith’s primary crushers are robust and designed to withstand the rigors of continuous operation. By integrating advanced technology and high-quality materials, Zenith ensures optimal efficiency and longevity, contributing to the overall productivity of the crushing plant.
Secondary Crushing: Achieving Desired Granularity
Following the primary crushing stage, the material is fed into secondary crushers for further reduction. This stage is focused on achieving more specific particle sizes and preparing the material for its final form. The secondary crushing process often involves the use of cone crushers, impact crushers, or hammer mills, each providing unique advantages depending on the material and desired outcome.
Zenith’s range of secondary crushers includes advanced models that offer precise control over the final product’s size and shape. Our cone crushers, for example, are engineered to deliver consistent performance, allowing operators to achieve uniform granularity. These crushers are equipped with hydraulic systems that offer precise adjustments, ensuring maximum efficiency and product quality.
Efficiency in secondary crushing is essential to maintain the flow of material through the plant. Zenith’s crushers are designed to integrate seamlessly with other stages, providing a smooth transition and maintaining production efficiency. Our comprehensive approach ensures that the secondary crushing stage is both efficient and effective, contributing to the overall success of the crushing plant.
Tertiary Crushing and Screening for Final Products
The tertiary crushing stage is the final step in the material reduction process, where the material is shaped and refined to meet specific product requirements. This stage often involves multiple crushers and screens to produce various product sizes and shapes. The aim is to produce high-quality aggregates that meet industry standards and customer specifications.
Zenith offers a variety of tertiary crushers, such as vertical shaft impactors (VSIs) and high-frequency screens, designed to deliver outstanding performance. Our VSIs are particularly effective in producing fine and uniformly shaped particles, making them ideal for applications requiring precision and consistency. Combined with our advanced screening solutions, these machines ensure that the final product is of the highest quality.
Screening is an integral part of this stage, separating the final products by size and removing any undesirable materials. Zenith’s high-frequency screens are designed to provide accurate and efficient screening, ensuring that only the best quality material proceeds to the final stages. By integrating advanced technology and robust design, Zenith ensures that the tertiary crushing and screening stage delivers optimal results.
In conclusion, the typical process flow of a crushing plant is a complex yet highly streamlined operation that converts raw materials into valuable products. Each stage, from primary crushing to tertiary crushing and screening, plays a crucial role in ensuring the efficiency and quality of the final output. Zenith’s range of crushers and screening equipment is designed to optimize each step of this process, offering unparalleled performance and reliability. By choosing Zenith, operators can rest assured that their crushing plant will operate at peak efficiency, delivering high-quality results every time.