Don't miss our holiday offer - 30% OFF!
What Materials Are Best For Jaw Crushers?
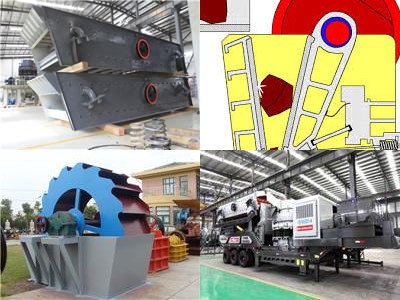
Jaw crushers are essential pieces of equipment in the mining and construction industries, used to crush and process various types of materials. The performance and durability of a jaw crusher greatly depend on the materials used in its construction. Selecting the right materials is crucial to ensure optimal efficiency, longevity, and cost-effectiveness of the equipment. In this article, we will delve into the importance of material selection for jaw crushers, key factors to consider when choosing materials, and a comparison of different materials to achieve the best performance.
Key Factors to Consider When Choosing Materials for Jaw Crushers
When selecting materials for jaw crushers, several key factors must be taken into account. Firstly, the material should have high strength and hardness to withstand the intense pressure and abrasion during the crushing process. Additionally, good impact resistance is essential to prevent fractures or deformations under heavy loads. Corrosion resistance is another crucial factor, especially when dealing with abrasive or corrosive materials. Moreover, the material should be easy to work with and maintain to ensure smooth operation and minimal downtime.
In terms of related products offered by Zenith company, we recommend exploring our range of high-quality jaw crusher materials designed to enhance the performance and longevity of your equipment. Our premium manganese steel jaw plates are known for their exceptional durability and wear resistance, making them ideal for demanding crushing applications. Additionally, our tungsten carbide inserts provide excellent abrasion resistance, extending the lifespan of the crushing components. For customers seeking superior performance and reliability, Zenith’s jaw crusher materials are the perfect choice.
Comparison of Different Materials for Optimal Jaw Crusher Performance
Various materials are used in the construction of jaw crushers, each with its unique properties and advantages. Common materials include manganese steel, high carbon steel, and tungsten carbide. Manganese steel is widely preferred for its high toughness and wear resistance, making it suitable for hard and abrasive materials. High carbon steel offers good strength and impact resistance, while tungsten carbide provides excellent wear resistance for extended durability. By comparing the properties of these materials, manufacturers and operators can select the most suitable option based on their specific needs and operating conditions.
In conclusion, the choice of materials for jaw crushers plays a critical role in determining the performance, efficiency, and lifespan of the equipment. By considering factors such as strength, hardness, impact resistance, and corrosion resistance, operators can ensure optimal operation and reduce maintenance costs. Zenith company offers a comprehensive range of jaw crusher materials tailored to meet the diverse needs of our customers. With our high-quality products and expertise in industrial equipment, we are committed to providing reliable solutions for enhancing crushing operations and maximizing productivity.