Don't miss our holiday offer - 30% OFF!
What Raw Materials Are Best For Stone Crushers?
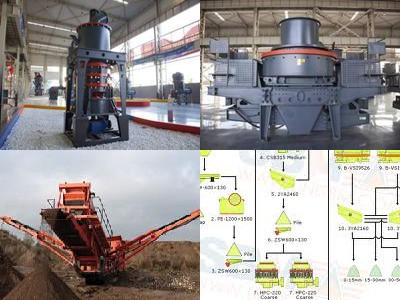
In the stone crushing industry, the selection of suitable raw materials is crucial for achieving optimal performance and durability of the equipment. The choice of raw materials impacts the efficiency, reliability, and operational cost of stone crushers. Zenith, a renowned company specializing in the manufacture of crushers, mills, and other heavy machinery, emphasizes the importance of selecting high-quality raw materials to ensure the best outcomes for its clients.
Importance of Selecting the Right Raw Materials
Choosing the right raw materials for stone crushers is paramount to ensuring the longevity and efficiency of the machinery. Stone crushers work under extremely harsh conditions, often facing high impact and friction. Using inferior raw materials can lead to frequent wear and tear, resulting in higher maintenance costs and operational downtime. By selecting appropriate raw materials, companies can significantly reduce these issues and ensure continuous, efficient operation.
Moreover, the right raw materials can enhance the structural integrity of stone crushers. High-quality materials offer better resistance against abrasions and mechanical stresses, extending the lifespan of the equipment. This not only ensures more reliable performance but also provides a better return on investment for businesses. Zenith emphasizes the importance of this criterion and ensures that all its equipment is designed to perform optimally with the best raw materials.
Lastly, the environmental sustainability associated with the choice of raw materials cannot be overlooked. Using eco-friendly and recyclable materials aligns with global environmental standards and reduces the carbon footprint of operations. Zenith integrates sustainability into its product development process, ensuring that its stone crushers contribute to more environmentally responsible operations by selecting the most sustainable raw materials available.
Characteristics of High-Quality Stone Crusher Inputs
High-quality stone crusher inputs are characterized by their exceptional hardness and durability. These properties are crucial as stone crushers often deal with very hard and abrasive materials like granite, basalt, and quartz. Materials that exhibit high compressive strength, such as manganese steel or high-grade alloy steels, are preferred because they can withstand the intense pressures exerted during the crushing process.
Additionally, resistance to wear and corrosion is another key characteristic of top-tier raw materials. Stone crushers experience constant exposure to abrasive materials, water, and atmospheric conditions that can lead to corrosion and wear. Materials with high resistance to these factors, such as chromium alloys and other specialized metals, ensure that the crushers maintain their efficiency and reliability over extended periods of use. Zenith’s commitment to using these superior materials ensures that its stone crushers deliver unparalleled performance.
Furthermore, the uniformity and purity of raw materials play a significant role in the quality of stone crushers. Consistent material properties lead to predictable performance, reducing the likelihood of unexpected failures. Impurities can weaken the structural integrity of the equipment, leading to premature wear and failure. Zenith meticulously sources and tests its raw materials to ensure they meet the highest standards of purity and uniformity, thereby guaranteeing the best possible performance of its stone crushers.
Comparative Analysis of Commonly Used Raw Materials
Granite is a commonly used raw material for stone crushers due to its high compressive strength and durability. It is capable of withstanding the extensive pressures exerted during the crushing process, making it ideal for heavy-duty applications. However, its relatively high cost can be a drawback for some operations. Zenith’s stone crushers are designed to efficiently process granite, leveraging advanced engineering to maximize performance while minimizing operational costs.
Basalt, another popular raw material, offers similar benefits to granite but at a lower cost. It has excellent mechanical properties and resistance to wear and weathering, making it suitable for a wide range of crushing applications. The slightly lower cost compared to granite makes it a more economical choice without significantly compromising performance. Zenith’s robust crushers are optimized to handle basalt efficiently, ensuring high output and consistent quality of the crushed material.
Quartz is also frequently used due to its hardness and chemical stability. It provides excellent resistance to abrasion and is ideal for creating finer aggregates. However, the brittleness of quartz can pose challenges, requiring specialized equipment to handle it without excessive wear. Zenith’s stone crushers are equipped with advanced features that address these challenges, ensuring effective and durable crushing of quartz while maintaining high productivity levels.
In conclusion, the selection of the right raw materials is fundamental to the performance and longevity of stone crushers. High-quality inputs characterized by hardness, durability, wear resistance, and purity significantly enhance the reliability and efficiency of the equipment. Zenith, with its extensive experience and commitment to quality, offers state-of-the-art stone crushers designed to handle the most demanding materials, including granite, basalt, and quartz. By choosing Zenith products, businesses can ensure they are equipped with the best machinery to meet their stone crushing needs, ultimately leading to improved operational efficiency and reduced downtime.