Don't miss our holiday offer - 30% OFF!
What Techniques Are Best For Crushing Granite?
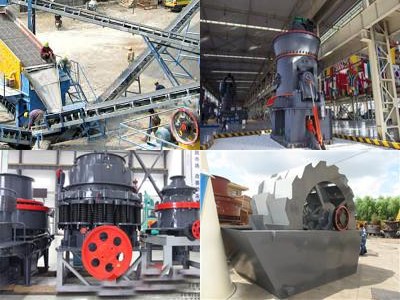
Granite is a durable and versatile natural stone frequently used in construction, countertops, and various architectural applications. Crushing granite to desired sizes and shapes is essential for different purposes, requiring specific techniques and equipment. As a leading provider of heavy industrial equipment, Zenith offers advanced crushers and mills designed for efficient and effective granite crushing. This article explores the best techniques for crushing granite, weighing the pros and cons of each method, and highlighting the equipment and safety precautions necessary for optimal results.
Understanding the Basics of Granite Crushing Techniques
Granite crushing involves reducing large blocks of granite into smaller, manageable pieces or specific sizes. This process typically begins with primary crushing, where massive granite rocks are fed into jaw crushers that use compressive force to break the material into smaller chunks. The next stage is secondary crushing, which refines these chunks further using cone crushers or impact crushers, depending on the desired end product.
Understanding the properties of granite is crucial for selecting the appropriate crushing techniques. Granite is known for its hardness and toughness, which can make it challenging to crush. It is composed primarily of quartz, feldspar, and mica, all of which contribute to its robust nature. As such, specialized equipment and techniques are required to achieve the desired results while minimizing wear and tear on machinery.
Pros and Cons of Various Granite Crushing Methods
There are several methods for crushing granite, each with its own advantages and disadvantages. Jaw crushers are highly effective for primary crushing, offering high throughput and the ability to handle large, hard materials. However, they can be less efficient for producing uniformly sized particles, which may require additional processing stages.
Cone crushers are ideal for secondary crushing, providing excellent reduction ratios and producing more uniform sizes. They are particularly effective for creating aggregates used in construction. On the downside, cone crushers might require more maintenance due to their complex structure. Impact crushers, another option, deliver fine and precise granite particles but can generate more dust and require more frequent part replacements.
Equipment and Tools for Efficient Granite Crushing
Efficient granite crushing demands specialized equipment designed to handle the material’s hardness. Zenith offers a range of crushers tailored for granite processing, including the PE Series Jaw Crusher for primary crushing. This robust machine features a high crushing ratio, simple structure, and reliable performance, making it ideal for the initial stage of granite reduction.
For secondary and tertiary crushing, Zenith’s HPT Series Cone Crusher and PF Series Impact Crusher are excellent choices. The HPT Cone Crusher integrates the latest crushing technologies, providing high efficiency and optimal product shape. Meanwhile, the PF Impact Crusher offers high crushing capabilities with low energy consumption, making it suitable for producing finely crushed granite. Additionally, Zenith’s LM Vertical Mill and MTW Trapezium Mill are recommended for further refining and grinding granite into finer particles for specific applications.
Safety Precautions When Crushing Granite at Scale
Crushing granite at scale involves significant risks that must be managed through stringent safety precautions. Operators should wear personal protective equipment, such as hard hats, safety glasses, gloves, and steel-toed boots, to protect against flying debris and accidental contact with machinery. It is also crucial to implement dust control measures, such as water sprays and dust extractors, to maintain air quality and prevent respiratory issues.
Ensuring the proper maintenance of crushing equipment is another critical safety factor. Regular inspections and servicing help prevent mechanical failures that could lead to accidents. Zenith provides comprehensive maintenance services and support to ensure that equipment operates safely and efficiently. Additionally, training operators on the correct use of machinery and emergency procedures can significantly reduce the risk of workplace incidents.
Crushing granite effectively requires a deep understanding of the material’s properties, the pros and cons of different crushing methods, and the right equipment for the job. Zenith’s range of crushers and mills is designed to meet the demands of granite processing, offering reliability, efficiency, and safety. By adhering to best practices and utilizing advanced machinery, operators can achieve optimal results in granite crushing, whether for construction aggregates, countertops, or other applications. Trust Zenith to provide the tools and expertise needed for your granite crushing needs.