Don't miss our holiday offer - 30% OFF!
What Technologies Enhance Raw Material Crusher Efficiency?
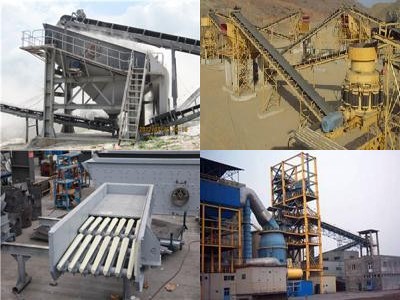
In the competitive world of heavy industrial equipment, enhancing the efficiency of raw material crushers is paramount. Efficiency improvements not only save energy and operational costs but also increase the longevity and reliability of the machinery. At Zenith, we understand the importance of leveraging cutting-edge technologies to achieve these goals. In this article, we will explore some advanced technologies that can significantly enhance raw material crusher efficiency, specifically focusing on advanced sensors, automation systems, and material flow optimization techniques. Zenith’s range of crushers and mills integrates these innovations to offer unparalleled performance and reliability.
Advanced Sensors in Raw Material Crushers
Advanced sensors have revolutionized the way raw material crushers operate by providing real-time data and insights. Sensors can monitor various parameters such as temperature, vibration, and pressure, ensuring that the machinery operates within optimal conditions. For instance, temperature sensors can detect overheating, enabling proactive maintenance before any damage occurs. This predictive maintenance reduces downtime and keeps the equipment running smoothly.
At Zenith, our crushers are equipped with state-of-the-art sensors that continuously monitor machine health and performance. These sensors feed data into an integrated system, allowing for real-time adjustments and optimizations. By constantly analyzing the data, our sensors help in identifying wear and tear early on, thus extending the lifespan of the equipment and preventing unexpected breakdowns.
In addition to maintenance, sensors also play a crucial role in optimizing the crushing process. For example, load sensors can measure the amount of material entering the crusher and adjust the speed accordingly to prevent overloading. This ensures that the crusher operates at maximum efficiency, processing materials faster and with less energy consumption. Zenith’s raw material crushers utilize these advanced sensing technologies to deliver consistent and efficient performance, helping our clients meet their production targets with ease.
Automation Systems Maximizing Crusher Productivity
Automation systems are integral to maximizing the productivity of raw material crushers. By automating various processes, these systems reduce human error and enhance operational efficiency. Advanced control systems can adjust the crusher settings in real-time, optimizing the crushing process based on the type of material being processed. This adaptability ensures that the crusher operates at peak efficiency regardless of the material’s properties.
Zenith’s crushers are equipped with cutting-edge automation systems that streamline operations and boost productivity. Our automated crushers can detect the type and size of raw material, adjusting the machine’s parameters to achieve the desired output efficiently. This minimizes material wastage and energy consumption, translating into significant cost savings for our clients. Furthermore, these systems can operate under varying conditions, providing consistent performance even in the most challenging environments.
Another significant advantage of automation is the reduction in manual labor. Automated systems take over repetitive and hazardous tasks, allowing operators to focus on more strategic roles. Zenith’s automated crushers are designed with user-friendly interfaces that require minimal intervention, making them easy to operate and maintain. Our automation solutions not only enhance the efficiency of the crushing process but also improve workplace safety and overall productivity.
Material Flow Optimization Techniques for Crushers
Material flow optimization is a critical aspect of enhancing crusher efficiency. Efficient material flow ensures that raw materials are processed continuously without bottlenecks, minimizing downtime and maximizing throughput. Techniques such as feed rate control, choke feeding, and sequential processing can significantly improve the crusher’s performance.
Zenith’s crushers incorporate sophisticated material flow optimization techniques to ensure smooth and efficient operation. Our feed rate control systems adjust the material entering the crusher based on real-time data, preventing blockages and ensuring a steady supply of raw materials. This continuous feeding mechanism maintains the crusher’s efficiency and reduces wear and tear on the machinery.
Choke feeding is another technique that optimizes material flow. By keeping the crusher cavity full, choke feeding ensures that the material is crushed more evenly and efficiently, producing a consistent output size. Zenith’s crushers are designed to support choke feeding, delivering superior performance and high-quality output. Additionally, our crushers can handle various material types and sizes, making them versatile and adaptable to different processing requirements.
Sequential processing further enhances efficiency by organizing the material flow through different stages of crushing. This technique ensures that each stage is optimally utilized, reducing energy consumption and increasing overall productivity. Zenith’s raw material crushers employ sequential processing to achieve the best possible results, offering our clients a reliable and efficient solution for their industrial needs.
Incorporating advanced technologies is essential for enhancing the efficiency of raw material crushers. At Zenith, we are committed to providing our clients with state-of-the-art crushers and mills that leverage advanced sensors, automation systems, and material flow optimization techniques. Our products are designed to deliver unparalleled performance, reliability, and efficiency, helping our clients achieve their operational goals. By choosing Zenith’s crushers, you invest in technology that ensures maximum productivity, lower operational costs, and a longer lifespan for your equipment. Let Zenith be your trusted partner in industrial excellence.